Под заплаха е половинвековна традиция в автомобилната индустрия
Toyota Motor Corp. натрупа ресурси от някои съставни елементи за четири месеца напред. Volkswagen AG построява шест завода, в които да създава акумулатори. Tesla Inc. се пробва да обезпечи достъпа си до първични материали. Веригата за доставки в автомобилната промишленост до момента бе извънредно ефикасна и се характеризираше с думите " тъкмо в точния момент ". Днес, повече от година след първите удари на пандемията по нея, тя минава през най-значимата си промяна от повече от половин век. През последните месеци автомобилните производители минаха през внезапни промени в търсенето, рискови естествени феномени и серия произшествия. Заради това те започнаха да слагат под въпрос признатата концепция, че постоянно могат да получат нужните елементи в нужния миг, написа The Wall Street Journal. " Последствията от безпрецендентната рецесия акцентира какъв брой уязвим е моделът ни ", разяснява Ашвани Гупта, основен действен шеф на Nissan Motor Co. Да вземем за образец Ford Motor Co. и най-популярния модел на компанията, F-150. Последната версия е цялостна с технологии и провокира впечатляващ интерес. През първите три месеца на 2021 година са продадени към 200 хиляди от модела в Съединени американски щати, най-хубавият резултат от 13 години. Но доставките изостават: заводите бяха затворени или не работиха на цялостен потенциал през април, а ситауцията ще остане по този начин най-малко доникъде на май. Това ще докара до $2,5 милиарда по-малка облага за Ford. Всичко това се случва поради дефицита на съставни елементи. Основната концепция зад модела " тъкмо в точния момент " е редуциране на разноските. Когато частите идват в завода няколко часа или дни преди да бъдат инсталирани върху автомобила, производителите не заплащат за това, което не употребяват: пестят от хранилища и хора, които да работят в тях. Моделът обаче е нежен, а рецесиите става все по-чести. Снежната стихия, която удари Тексас в средата на февруари, затвори рафинерията, която е виновна за 85% от създадените в Съединени американски щати синтетични смоли. Тези смоли се употребяват в разнообразни съставни елементи на колите като броните, кормилата и седалките. Смолата е измежду най-евтините сурови материали, употребявани в производството на един автомобил, само че дилърите не могат да продават коли без седалки. В края на март Toyota спря производството в няколко американски завода поради дефицита, съгласно информация на изданието, което засегна някои от най-популярните модели, в това число RAV4. В опит да се оправят със обстановката, снабдители започнаха да внасят смоли от Европа, споделя Шелдън Клайн, юрист в Butzel Long, която е консултант на някои от фирмите в промишлеността. " Икономически, това е съкрушаващо ", споделя той. Мениджърите от автомобилната промишленост са безапелационни, че не желаят напълно да сменят модела " тъкмо в точния момент " поради големите разноски, които той икономисва. Но до избрана степен те стартират да трансформират тактиката, коцентрирайки се върху материалите, при които се усещат най-уязвими. Компаниите се пробват да се запасят с най-критичните съставни елементи, изключително в случай че са леки и относително евтини (но незаменими) като полупроводниците. Главният изпълнителен шеф на Ford Джим Фарли удостовери, че компанията желае да се ресурси с чипове. " Редица други промишлености имат буфери за сериозни съставни елементи като чиповете. И доста от тези компании заплащат за тях авансово, даже с години ". Преходът към електрически коли усилва натиска върху производителите да премислят половинвековната тактика, тъй като новият вид задвижване изисква повече елементи, при които предлагането е по-ниско — в това число литиево-йонни акумулатори и полупроводници. General Motors и LG Chem построяват цех на стойност $2,3 милиарда в Охайо и търсят уместно място за втори подобен. Фабриките ще създават акумулатори за плануваните стотици хиляди електрически автомобили. Volkswagen, въпреки да възнамерява шест завода за акумулатори, ще направи обособена поръчка за $14 милиарда до 2030 година Компаниите се учат от Tesla, която пък е повлияна от Силициевата котловина и която построи цех за акумулатори за $5 милиарда дружно с Panasonic. Разбира се, обезпечаването на лично произвеждане на акумулатори надалеч не позволява всички проблеми: даже и най-футуристичните модели ще се нуждаят от пластмаса, гуми, кожа. Въпреки това Tesla се пробва да разпознава най-стратегическите материали и да си ги обезпечава сама — нещо, което останалите производители оставят на доставчиците си. През септември компанията подписа договорка, която ще ѝ даде достъп до лития от мина в Северна Каролина. Миналата година основният изпълнителен шеф Илън Мъск съобщи, че желае да купува и никел непосредствено. Стратегията на Tesla да преследва непосредствено суровините връща автомобилната промишленост един век насам във времето, когато Хенри Форд полагаше основите на своята империя с новаторските си индустриални похвати. През 20-те години на предишния век Ford се гордееше с отвесната си интеграция, с контрола върху всичко належащо за производството на един автомобил. Заводът в Мичиган произвеждаше освен коли, само че и стоманата за тях, която идваше от личните мини на компанията. След кончината на Форд компанията трансформира модела. Производителите тогава взимат решение, че е по-ефективно да оставят стоманата на фирмите, които познават този бизнес най-добре. При производството на един автомобил стана по-важно точните елементи да бъдат купени. Toyota направи идната стъпка. Историята споделя, че един ден през 1950 година мениджърът Таичи Охно посещава американски супермаркет и се впечатлява по какъв начин рафтовете са непрекъснато цялостни, спомня си Джефри Лайкър в книгата си The Toyota Way. Клиентите са щастливи и намират всичко належащо, макар че магазините имат дребен склад — за разлика от големите пространства на автомобилните производители, цялостни с всичко належащо от стомана до гуми. Супермаркетите нямат необикновен избор, защото не могат да се презапасят с банани за месеци напред. Но въпреки всичко, открива Охно, тази процедура отстрани разноски. Така Toyota взема решение, че ще заплаща и получава единствено нужните елементи за колите, които ще бъдат съединени в същия ден. И по този начин ще могат да понижат размера на заводите и складовете. За Toyota задачата не е сложна с помощта на лоялните снабдители със хранилища към заводите. Американските съперници, въпреки и скептични и внимателни първоначално, поемат по същия път, защото системата се оказва ефикасна. По-късно и доставчиците вършат същото с техните поддоставчици. Идеята набира скорост и в други промишлености. Apple, McDonald " s и даже Target употребяват някакъв вид на модела и през днешния ден. Понякога системата отхвърля — като при събития като 11-ти септември — само че промишлеността вдигаше плещи и продължаваше. Полъхът на смяната стартира да се усеща доскоро повече от десетилетие, когато най-малко 50 автомобилни доставчика в Съединени американски щати банкрутираха и оставиха производителите с пръст в уста. През 2011 година мощното земетресение в Япония спря работата на редица снабдители на Toyota, в това число на Renesas. Тогава компанията принуди доставчиците си да разкрият кой им продава съставни елементи — голямо изпитание в промишлеността, в която доставчиците пазят в загадка фирмите, с които работят, от боязън, че производителите ще ги прескочат, с цел да понижат разноските. С течение на времето Toyota построява база данни, която покрива 400 хиляди съставния елемент. За някои от тези съставни елементи Toyota желае от доставчиците си да се презапасят — антитезата на " тъкмо в точния момент ". Така Denso Corp., най-големият снабдител на японския производител, покачва запасите си към края на март 2020 година и те към този момент са задоволителни за 50 дни — при 38 дни през 2011 година Усилията на Toyota помогнаха да компанията да се оправи по-лесно с тазгодишния дефицит на полупроводници, въпреки че не липсваха провокации. Същият цех на Renesas, който бе ударен от земетресение преди десетилетие, спря работа през март поради пожар и няма да успее да възвърне изцяло активността си до юли.
Източник: dnesplus.bg
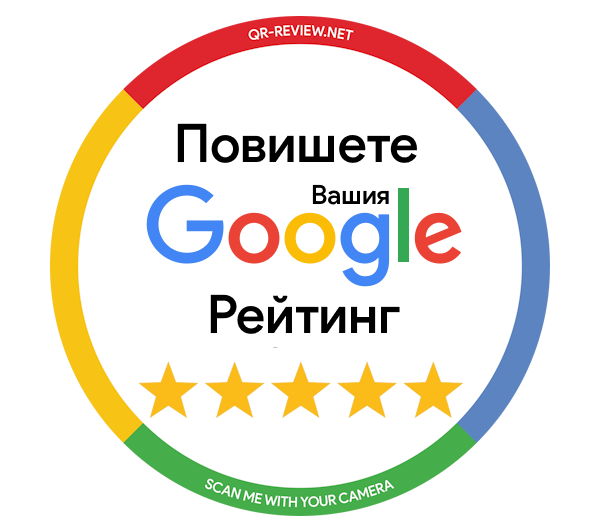

КОМЕНТАРИ