В производствената си система BMW Group разчита все повече на индивидуални роботи-грайфери създадени с 3D печат
+++ Бързо, преференциално, гъвкаво и стабилно с Additive Manufacuturing
+++ Новите бионични захващачи (или грайфери) в завода на BMW Group в Ландсхут пестят тегло
+++ Иновативни бионични грайфери за цялостни каросерии в завода на BMW Group в Мюнхен
С над 30 години опит, BMW Group е пионер в региона на Additive Manufacturing, по-известно като 3D принтиране. След като обособени елементи и съставни елементи на транспортни средства се създават от 3D принтери от 1991 година насам, в началото за концептуални коли, прототипи и спортни коли, а по-късно и за серийни модели, BMW Group създава и многочислени работни помощни средства и принадлежности за личната си индустриална система, употребявайки разнообразни процеси на 3D щемпел. От в началото направени по поръчка ортези за чиновници до измервателни уреди и индустриални помощни средства, в този момент това се разгръща до огромни захващащи устройства за роботи с усъвършенствано тегло, да вземем за пример за CFRP покриви и цели подови групи на каросерията. В „ Additive Manufacturing Campus “ в Обершлайсхайм, където BMW Group сплотява произвеждане, проучвания и образование за 3D принтиране под един покрив, през 2023 година са „ отпечатани “ над 300 000 елементи. Към тях през последните години се прибавят и над 100 000 печатни елементи във всички фабрики в световната индустриална мрежа, от Спартанбург до локациите в Германия и Азия.
„ Увеличеното потребление на Additive Manufacturing в индустриалната система на BMW Group носи голям брой преимущества. Например, ние сме в положение да произвеждаме наши лични помощни средства за произвеждане и манипулационни грайфери бързо, рентабилно, гъвкаво и благодарение на устойчиви материали, които можем да приспособяваме самостоятелно към нашите потребности когато и да е и да ги проектираме по този начин, че да бъдат усъвършенствани във връзка с тежестта. По-малкото тегло разрешава по-високи скорости на линията, кратко време на цикъла и понижени разноски. Освен това в средносрочен проект могат да се употребяват по-малки роботи, което също понижава излъчванията на CO2 и разноските “, сподели Йенс Ертел, началник на „ Additive Manufacturing Campus “.
„ В допълнение към директните Additive Manufacturing процеси, BMW Group от доста години употребява 3D щемпел с пясък за основаване на леярски форми в своята локация в Ландсхут. Тази технология обичайно се употребява за произвеждане на ляти прототипи, както и в крупносерийното произвеждане на съставни елементи за High Performance мотори. Друга извънредно привлекателна област на приложение е потреблението на широкоформатни помощни средства за произвеждане, ” сподели Клаус Замер, началник на продуктовото и процесното обмисляне за леене на леки метали.
Печатни форми за отливане на алуминиеви цилиндрови глави в огромни серии
Процесите на адитивно произвеждане се употребяват от дълго време в завода на BMW Group в Ландсхут. В продължение на дълги години това включва формите за произвеждане на алуминиеви цилиндрови глави, които се отпечатват триизмерно посредством процеса на пясъчно леене. Пясъкът се нанася неведнъж на тънки пластове и се свързва благодарение на свързващо вещество. Това значи, че могат да бъдат основани и леярски форми за произвеждане на доста комплицирани структури, които по-късно се пълнят с полутечен алуминий.
Производство на широкомащабни робот и-грайфери за покриви от CFRP посредством 3D принтиране
От няколко години Центърът за леки структури и технологии на BMW Group в Ландсхут също употребява изключително огромен детайл за захващане, който е основан посредством развой на 3D принтиране. Грайферът за робот, който тежи към 120 кг, може да бъде създаден единствено за 22 часа и по-късно се употребява на пресата при производството на всички CFRP покриви за моделите на BMW M GmbH. Първо, пресата се зарежда със суровината CFRP. За да се извадят готовите покриви, грайферът просто се завърта на 180 градуса. В съпоставяне с стандартните грайфери, версията, създадена благодарение на 3D щемпел, е с към 20 % по-лека, което удължава потребния живот на роботите и понижава износването и интервалите на поддръжка на системите. Комбинираното потребление на две работни стъпки също редуцира цикъла. Уникално качество на робота-захващач е идеалната композиция от два разнообразни процеса на 3D щемпел. Докато вакуумните захващащи устройства и държачите на иглените захващащи устройства за задържане на CFRP суровината са основани посредством селективно лазерно синтероване (SLS), огромната покривна черупка и носещата структура се създават посредством широкомащабен щемпел (LSP). При LSP съставените елементи с огромна повърхност могат да бъдат създавани рентабилно и стабилно. Използват се гранули за леене под налягане и рециклирани пластмаси, а остатъците от CFRP също могат да се употребяват и рециклират. В съпоставяне с потреблението на първоначални първични материали, излъчванията на CO2 по време на производството на грайфера са по-ниски с над 60%.
Допълнително намаление на тежестта посредством ново потомство бионични грайфери
През лятото на 2023 година е показано ново, още по-леко потомство грайфери. За тази цел предходната идея за захващане е оценена и топологично усъвършенствана – по този начин се ражда бионичния робот за захващане. Той съчетава покривната обвивка от LSP принтера със SLS вендузи и бионична усъвършенствана поддържаща конструкция. За задачата при пясъчното леене се употребява шаблон с отпечатани ядра, с които се отлива филигранната алуминиева структура. Новият грайфер икономисва спомагателни 25 % от тежестта спрямо предшественика си, което значи, че целият индустриален развой за CFRP покрив за BMW M3 може да се извърши единствено от един робот вместо с предходните три. Заводът на BMW Group в Ландсхут в този момент употребява двойни грайфери за всички CFRP покриви, които са създадени самостоятелно с
Нови грайфери, основани благодарение на 3D щемпел, и при производството на каросерии
BMW Group също по този начин към този момент употребява захващащи устройства, основани посредством 3D принтиране, и при производството на каросерии, да вземем за пример захващащи устройства, отпечатани благодарение на процеса LSP за ръководство на порти в завода на BMW Group в Регенсбург. „ Чрез потребление на усъвършенствана носеща конструкция от 3D принтиране, ние успяхме да увеличим твърдостта на ръкохватката при боравене с детайлите на вратата в завода в Регенсбург и в това време да понижим тежестта. Това значи, че роботи с ниска товароносимост могат да се употребяват в следващи планове, което спомага за понижаване на разноските “, изяснява Флориан Рийбел, началник произвеждане на порти и капаци в Регенсбург.
В завода на BMW Group в Мюнхен компанията отива една крачка напред. Наскоро в главния цех бяха въведени първите екземпляри на бионичен робот-грайфер, който може да хваща и движи цялото дъно на BMW i4. За захващащото устройство на дъното се основава леярска форма в пясък благодарение на 3D щемпел, която се цялостни с течен алуминий. Носачът е усъвършенстван във връзка с тежестта и оптималната си товароносимост и с всички спомагателни детайли тежи единствено 110 кг. Това го прави към 30 % по-лек от предходния стандартен модел. Производството с пясъчно леене и алуминий дава опция за произвеждане на усъвършенствани филигранни структури, усъвършенствани във връзка с натоварването. Това води до оптимално понижаване на тежестта и в средносрочен проект разрешава потреблението на по-малки и по-леки тежкотоварни роботи, които изискват по-малко сила и по този метод понижават излъчванията на CO2.
Маркус Леман, началник на отдела за редовно инженерство и роботика в завода на BMW Group в Мюнхен, сподели: „ В завода в Мюнхен ние непрестанно разширяваме потреблението на адитивно създадени спомагателни средства за произвеждане. В региона на системите за захващане и манипулиране ние използваме 3D щемпел, с цел да оборудваме нашите наложили се захващащи устройства с самостоятелни, отпечатани спомагателни детайли и към този момент сме заменили цялостни системи за захващане с високо интегрирани и усъвършенствани във връзка с тежестта опорни структури. При обработката на цялото дъно на каросерията на BMW i4 успяхме да понижим тежестта с 30 %, а за целия грайфер с над 50. “
Използване на новаторски софтуерни решения при Additive Manufacturing
Проектирането и изчисляването на филигранни и бионични структури се прави благодарение на специфични, генерични софтуерни принадлежности, да вземем за пример Synera. BMW iVentures са вложили стратегически в този програмен продукт, по-рано наименуван Elise. Synera разрешава бърза и ефикасна оптимизация и в този момент се употребява в доста развойни области на BMW Group. Използването на софтуера е изключително потребно при 3D принтиране, защото топологично усъвършенстваните бионични структури могат да бъдат отпечатани съвсем едно към едно с помощта на високата степен на независимост на 3D принтирането. Това значи, че може да се употребява цялостният капацитет за олекотяване на структурата. В Additive Manufacturing Campus на BMW Group екип от експерти по дизайн и конструиране съпоставя огромно многообразие от софтуерни решения и ги употребява за планиране на съставни елементи. Опитът във връзка с 3D принтиране се преподава от Additive Manufacturing Campus в цялата компания. В съответния случай на приложение при дизайна на грайферите бяха създадени и приложени специфични работни процеси, които значително автоматизират изчисляването и проектирането на носещата структура и с помощта на това го осъществят бързо и дейно.
*Източник: www.bmw.bg
+++ Новите бионични захващачи (или грайфери) в завода на BMW Group в Ландсхут пестят тегло
+++ Иновативни бионични грайфери за цялостни каросерии в завода на BMW Group в Мюнхен
С над 30 години опит, BMW Group е пионер в региона на Additive Manufacturing, по-известно като 3D принтиране. След като обособени елементи и съставни елементи на транспортни средства се създават от 3D принтери от 1991 година насам, в началото за концептуални коли, прототипи и спортни коли, а по-късно и за серийни модели, BMW Group създава и многочислени работни помощни средства и принадлежности за личната си индустриална система, употребявайки разнообразни процеси на 3D щемпел. От в началото направени по поръчка ортези за чиновници до измервателни уреди и индустриални помощни средства, в този момент това се разгръща до огромни захващащи устройства за роботи с усъвършенствано тегло, да вземем за пример за CFRP покриви и цели подови групи на каросерията. В „ Additive Manufacturing Campus “ в Обершлайсхайм, където BMW Group сплотява произвеждане, проучвания и образование за 3D принтиране под един покрив, през 2023 година са „ отпечатани “ над 300 000 елементи. Към тях през последните години се прибавят и над 100 000 печатни елементи във всички фабрики в световната индустриална мрежа, от Спартанбург до локациите в Германия и Азия.
„ Увеличеното потребление на Additive Manufacturing в индустриалната система на BMW Group носи голям брой преимущества. Например, ние сме в положение да произвеждаме наши лични помощни средства за произвеждане и манипулационни грайфери бързо, рентабилно, гъвкаво и благодарение на устойчиви материали, които можем да приспособяваме самостоятелно към нашите потребности когато и да е и да ги проектираме по този начин, че да бъдат усъвършенствани във връзка с тежестта. По-малкото тегло разрешава по-високи скорости на линията, кратко време на цикъла и понижени разноски. Освен това в средносрочен проект могат да се употребяват по-малки роботи, което също понижава излъчванията на CO2 и разноските “, сподели Йенс Ертел, началник на „ Additive Manufacturing Campus “.
„ В допълнение към директните Additive Manufacturing процеси, BMW Group от доста години употребява 3D щемпел с пясък за основаване на леярски форми в своята локация в Ландсхут. Тази технология обичайно се употребява за произвеждане на ляти прототипи, както и в крупносерийното произвеждане на съставни елементи за High Performance мотори. Друга извънредно привлекателна област на приложение е потреблението на широкоформатни помощни средства за произвеждане, ” сподели Клаус Замер, началник на продуктовото и процесното обмисляне за леене на леки метали.
Печатни форми за отливане на алуминиеви цилиндрови глави в огромни серии
Процесите на адитивно произвеждане се употребяват от дълго време в завода на BMW Group в Ландсхут. В продължение на дълги години това включва формите за произвеждане на алуминиеви цилиндрови глави, които се отпечатват триизмерно посредством процеса на пясъчно леене. Пясъкът се нанася неведнъж на тънки пластове и се свързва благодарение на свързващо вещество. Това значи, че могат да бъдат основани и леярски форми за произвеждане на доста комплицирани структури, които по-късно се пълнят с полутечен алуминий.
Производство на широкомащабни робот и-грайфери за покриви от CFRP посредством 3D принтиране
От няколко години Центърът за леки структури и технологии на BMW Group в Ландсхут също употребява изключително огромен детайл за захващане, който е основан посредством развой на 3D принтиране. Грайферът за робот, който тежи към 120 кг, може да бъде създаден единствено за 22 часа и по-късно се употребява на пресата при производството на всички CFRP покриви за моделите на BMW M GmbH. Първо, пресата се зарежда със суровината CFRP. За да се извадят готовите покриви, грайферът просто се завърта на 180 градуса. В съпоставяне с стандартните грайфери, версията, създадена благодарение на 3D щемпел, е с към 20 % по-лека, което удължава потребния живот на роботите и понижава износването и интервалите на поддръжка на системите. Комбинираното потребление на две работни стъпки също редуцира цикъла. Уникално качество на робота-захващач е идеалната композиция от два разнообразни процеса на 3D щемпел. Докато вакуумните захващащи устройства и държачите на иглените захващащи устройства за задържане на CFRP суровината са основани посредством селективно лазерно синтероване (SLS), огромната покривна черупка и носещата структура се създават посредством широкомащабен щемпел (LSP). При LSP съставените елементи с огромна повърхност могат да бъдат създавани рентабилно и стабилно. Използват се гранули за леене под налягане и рециклирани пластмаси, а остатъците от CFRP също могат да се употребяват и рециклират. В съпоставяне с потреблението на първоначални първични материали, излъчванията на CO2 по време на производството на грайфера са по-ниски с над 60%.
Допълнително намаление на тежестта посредством ново потомство бионични грайфери
През лятото на 2023 година е показано ново, още по-леко потомство грайфери. За тази цел предходната идея за захващане е оценена и топологично усъвършенствана – по този начин се ражда бионичния робот за захващане. Той съчетава покривната обвивка от LSP принтера със SLS вендузи и бионична усъвършенствана поддържаща конструкция. За задачата при пясъчното леене се употребява шаблон с отпечатани ядра, с които се отлива филигранната алуминиева структура. Новият грайфер икономисва спомагателни 25 % от тежестта спрямо предшественика си, което значи, че целият индустриален развой за CFRP покрив за BMW M3 може да се извърши единствено от един робот вместо с предходните три. Заводът на BMW Group в Ландсхут в този момент употребява двойни грайфери за всички CFRP покриви, които са създадени самостоятелно с
Нови грайфери, основани благодарение на 3D щемпел, и при производството на каросерии
BMW Group също по този начин към този момент употребява захващащи устройства, основани посредством 3D принтиране, и при производството на каросерии, да вземем за пример захващащи устройства, отпечатани благодарение на процеса LSP за ръководство на порти в завода на BMW Group в Регенсбург. „ Чрез потребление на усъвършенствана носеща конструкция от 3D принтиране, ние успяхме да увеличим твърдостта на ръкохватката при боравене с детайлите на вратата в завода в Регенсбург и в това време да понижим тежестта. Това значи, че роботи с ниска товароносимост могат да се употребяват в следващи планове, което спомага за понижаване на разноските “, изяснява Флориан Рийбел, началник произвеждане на порти и капаци в Регенсбург.
В завода на BMW Group в Мюнхен компанията отива една крачка напред. Наскоро в главния цех бяха въведени първите екземпляри на бионичен робот-грайфер, който може да хваща и движи цялото дъно на BMW i4. За захващащото устройство на дъното се основава леярска форма в пясък благодарение на 3D щемпел, която се цялостни с течен алуминий. Носачът е усъвършенстван във връзка с тежестта и оптималната си товароносимост и с всички спомагателни детайли тежи единствено 110 кг. Това го прави към 30 % по-лек от предходния стандартен модел. Производството с пясъчно леене и алуминий дава опция за произвеждане на усъвършенствани филигранни структури, усъвършенствани във връзка с натоварването. Това води до оптимално понижаване на тежестта и в средносрочен проект разрешава потреблението на по-малки и по-леки тежкотоварни роботи, които изискват по-малко сила и по този метод понижават излъчванията на CO2.
Маркус Леман, началник на отдела за редовно инженерство и роботика в завода на BMW Group в Мюнхен, сподели: „ В завода в Мюнхен ние непрестанно разширяваме потреблението на адитивно създадени спомагателни средства за произвеждане. В региона на системите за захващане и манипулиране ние използваме 3D щемпел, с цел да оборудваме нашите наложили се захващащи устройства с самостоятелни, отпечатани спомагателни детайли и към този момент сме заменили цялостни системи за захващане с високо интегрирани и усъвършенствани във връзка с тежестта опорни структури. При обработката на цялото дъно на каросерията на BMW i4 успяхме да понижим тежестта с 30 %, а за целия грайфер с над 50. “
Използване на новаторски софтуерни решения при Additive Manufacturing
Проектирането и изчисляването на филигранни и бионични структури се прави благодарение на специфични, генерични софтуерни принадлежности, да вземем за пример Synera. BMW iVentures са вложили стратегически в този програмен продукт, по-рано наименуван Elise. Synera разрешава бърза и ефикасна оптимизация и в този момент се употребява в доста развойни области на BMW Group. Използването на софтуера е изключително потребно при 3D принтиране, защото топологично усъвършенстваните бионични структури могат да бъдат отпечатани съвсем едно към едно с помощта на високата степен на независимост на 3D принтирането. Това значи, че може да се употребява цялостният капацитет за олекотяване на структурата. В Additive Manufacturing Campus на BMW Group екип от експерти по дизайн и конструиране съпоставя огромно многообразие от софтуерни решения и ги употребява за планиране на съставни елементи. Опитът във връзка с 3D принтиране се преподава от Additive Manufacturing Campus в цялата компания. В съответния случай на приложение при дизайна на грайферите бяха създадени и приложени специфични работни процеси, които значително автоматизират изчисляването и проектирането на носещата структура и с помощта на това го осъществят бързо и дейно.
*Източник: www.bmw.bg
Източник: auto-press.net
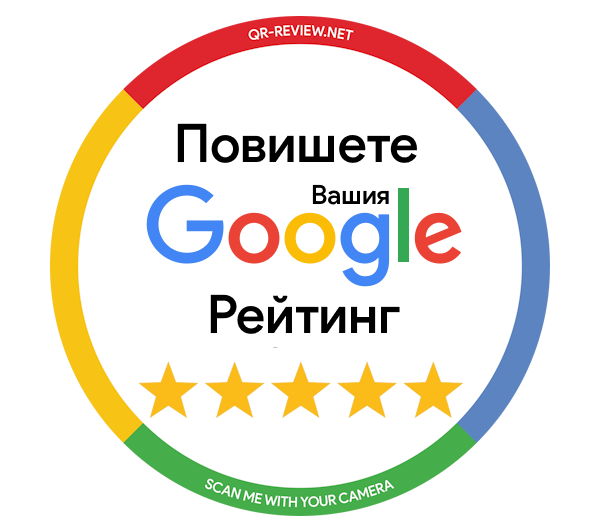

КОМЕНТАРИ