Ще ми отпечаташ ли печатница?
[Shutterstock] Изследователите са уверени, че потреблението на огромни 3D принтери в корабостроенето доста ще понижи индустриалните разноски и времето за основаване на нови плавателни съдове. Корабостроенето е досадно и скучно занятие, даже когато става дума за дребни плавателни съдове, направени от съвременни материали, като да вземем за пример фибростъкло, а не за дървена лодка. Първо би трябвало да извършите шаблон на корпуса. След това вътре полагате пласт след пласт смола и стъклени влакна. Накрая изваждате готовата структура и се захващате с довършителните работи. Тези действия могат да лишават месеци...
Всичко това обаче скоро може да се промени. Изследователи от университета в Мейн сега организират тествания с 8-метрова патрулна лодка, основана от нулата единствено за 72 часа. Те реализират това, употребявайки великански 3D принтер.
Абонирайте се за Капитал Четете безкрайно и подкрепяте напъните ни да пишем по значимите тематики Откакто влизат в комерсиално произвеждане през 90-те години на предишния век, 3D принтерите по принцип се употребяват за основаването на дребни предмети като прототипи, съставни елементи за реактивни мотори или зъбни коронки. В момента идва ред на устройствата с големи размери. Те са способни да отпечатват доста по-големи обекти, в сравнение с беше допустимо до момента. И го вършат по-бързо.
За да основат патрулната лодка за потребностите на американската войска, екипът в Мейн работи в съдействие с Националната лаборатория Оук Ридж в Тенеси, която оказва помощ в създаването на процеса по триизмерно печатане и с компанията Ingersoll Machine Tools в Илинойс, която конструира самия принтер. Изследователите от университета са уверени, че потреблението на сходни огромни устройства в корабостроенето ще понижи доста индустриалните разноски и времето за основаване на нови плавателни съдове.
Размерът има значение
Максималният размер на обекта, който може да бъде генериран от даден 3D принтер, се дефинира от размера на самите отпечатващи устройства. В момента множеството от тях са най-вече с размерите на домакински ледник.
През последните няколко години инженерите опитват с разнообразни начини за реализиране на по-големи мащаби при триизмерното печатане, като инсталират механизма върху външно скеле. За жал крайният резултат нормално е постепенно и непрецизно устройство, което генерира груби обекти, нуждаещи се от доста спомагателна и скъпа ръчна обработка.
Учените от университета в Мейн обаче преодоляват този проблем. Те инсталират дюзата, която поставя пластовете от " 3D мастилото ", върху рамка на подемен кран. Самото мастило съставлява разтопена термопластична смола, съдържаща карбонови влакна. Контролирана благодарение на мощен компютър, дюзата се движи хоризонтално (както при всеки развой по триизмерно принтиране) и построява стремежи обект, като генерира тъничък пласт от субстанцията, изчаква го да се втвърди, издига се малко нагоре, поставя още смола и продължава по този метод, до момента в който реализира окончателната форма.
Всичко това може да бъде реализирано със забележителна скорост. Принтерът, конструиран от университета в Мейн, е кадърен да употребява до 70 кг термопластична смола на час. В момента той може да основава предмети с дължина 30 метра, широчина 7 м и височина 3 м. Тези пропорции обаче елементарно могат да бъдат увеличени, като устройството се инсталира на по-голям подемен кран. Също по този начин върху преносимата част, където е инсталирана дюзата, може да се добави и автоматизирана фреза, която да отстранява грапавините и да изглажда повърхността.
След като към този момент са създали технологията, сега учените се пробват да подобрят естеството на триизмерното " мастило ", тъй че да го създадат по-щадящо околната среда. Вместо да употребяват карбонови влакна, те считат да се извърнат към отпадъчната целулоза като сурогат. Подобно решение би спечелило поддръжката на " зелените " деятели, защото карбоновите влакна нормално се създават въз основата на петролни артикули. Хабиб Агхер, който е един от ръководителите на плана, твърди, че задачата е градивната субстанция за печатане да е най-малко 50% на основата на дървесни артикули. Според него по този начин може да се сътвори композитна сплав, която е съизмерима като издръжливост и тегло с алуминия. В близко бъдеще откривателите също по този начин се надяват да могат да поставят до 230 кг 3D мастило на час. Последното им достижение е отпечатването на отливка за основаването на тавана на лодка. За задачата са употребявани целулозни влакна и смола, извлечена от царевични боклуци. И с цел да има спомагателен " зелен " резултат, матрицата може да бъде рециклирана и материалите да се употребяват наново.
Просто натисни print
Създаването на отливки и индустриални принадлежности ще е значимо приложение на огромните 3D принтери, твърди доктор Крейг Блу, шеф по енергийната успеваемост в лабораторията " Оук Ридж ". Производството на принадлежности е скъпа активност заради две аргументи. То изисква профилирани умения, а също така предметите се създават в единични бройки или дребни количества, тъй че не може да се реализира спестовност от мащаба. При триизмерните принтери обаче цената на численост е почти една и съща, без значение дали произвеждаш един или доста предмети.
Технологията предлага и други преимущества. Например принтерът, конструиран от " Оук Ридж ", е употребен от подизпълнители за основаване на особено завършени матрици за бетонни отливки върху фасадата на 45-етажна постройка, издигната на мястото на остарелия захарен цех в Бруклин, Ню Йорк. По принцип сходни матрици се вършат от дърво. За основаването им се наемат експерти, който ги създават ръчно. Въпросните дървени матрици обаче не са изключително издръжливи и се амортизират след 3-4 бетонни отливки. Според доктор Блу обаче 3D отпечатаните аналози, направени от подсилени карбонови влакна, могат да устоят до 200 заливания с цимент.
Лабораторията " Оук Ридж " също по този начин работи по технология, която разрешава директното печатане на бетонни структури. Но защото би трябвало да се употребяват големи 3D принтиращи подемни кранове, основаването на небостъргачи и други сходни уреди с огромни размери явно би трябвало да става не на веднъж, а на части. Отпечатването на бетонни секции в следена фабрична среда и по-късно сглобяването им на място евентуално ще се окаже по-подходящо, изключително когато става дума за направа на комплицирани артистични структури.
Това е методът, общопризнат от Сю Вайгуо и сътрудниците му от университета " Цинхуа " в Пекин. Те употребяват чифт роботизирани " ръце ", посредством които генерират сглобяеми секции от цимент, разбъркан с полиетиленови нишки. След това бетонните панели са употребявани за построяването на 26-метров пешеходен мост над езеро в индустриалната зона на Шанхай. Съоръжението е конструирано по този начин, че да прилича моста " Анджи " – каменна арка над река Киаохе, провинция Хебей, датираща от към 600 година сл. н.е. Репликата на античния мост е отпечатана за към 450 часа. Това е много умерено движение по стандартите на 3D принтера, употребен в корабостроителницата в Мейн, само че много бързо на фона на 10-те години, които са били нужни за построяването на оригинала, и даже спрямо бързината на актуалната строителна промишленост. Изследователите са пресметнали, че индустриалните разноски са били към 2/3 от цената на аналогично оборудване, направено благодарение на стандартен способи. Най-трудната задача, с която 3D принтирането се сблъсква, е основаването на обекти от метал.
Все по-големи обекти и по-висока скорост на печатане се реализират и посредством други технологии за 3D принтиране. Чад Миркин и сътрудниците му в Северозападния университет в Илинойс са създали способ, наименуван high-area rapid printing (HARP). Тяхното устройство е способно да основава обекти с повърхност на основата към един квадратен метър и височина 4 м. То реализира това, като последователно " изтегля " плътния обект от дребен басейн, цялостен с течен полимер.
Въпросният принтер е основан на действителен индустриален развой, само че в по-големи мащаби. При него течният полимер се съхранява в съд с транспарантна основа. Всеки пласт от предмета, който би трябвало да бъде отпечатан, се прожектира през нея с ултравиолетови лъчи. Те от своя страна провокират химична реакция и сгъстяване на полимера в нужната форма. Готовият пласт се захваща за апарат, спуснат към повърхността на течната субстанция, и се изтегля нагоре. Процедурата се повтаря, до момента в който целият подготвен обект не бъде изтеглен от басейна с течен полимер.
Иновацията, която HARP прибавя към този развой, е прибавянето на тъничък филм от смазка, който тече по повърхността на транспарантната основа. Според откривателите субстанцията прилича течен тефлон и пречи на полимерите да се залепят за долната част на басейна, а също по този начин лишават топлината, която се генерира при ултравиолетовото сгъстяване. Крайният резултат от това е, че 3D принтерът е кадърен да работи доста по-бързо от преди. Според доктор Миркин той може да сътвори за няколко часа обект с размерите на възрастен човешки субект. Ако употребявате стандартен тримерен принтер, същото би лишило няколко дни.
Процесът HARP разрешава потреблението на необятен диапазон от материали за печатане в огромен мащаб – става дума за стотици типове разнообразни полимери, които могат да основават твърди, меки или пък гумени обекти. С него могат да се отпечатват и предмети от смоли, съдържащи материали като силициев карбид, който може да се трансформира в твърди термоустойчиви керамични сплави. Компоненти, направени от сходен материал, могат да бъдат употребявани в най-различни промишлености – изработката на коли, самолети, даже и здания. Технологията може да бъде употребена и в още по-големи мащаби, прибавя доктор Миркин. Той също по този начин е съосновател на компанията Azul 3D, която се пробва да комерсиализира процеса HARP. Според неговите упования първите принтери, употребяващи тази технология, ще се появят на пазара след към 18 месеца.
Хеви метъл
Най-трудната задача, с която 3D принтирането се сблъсква, е основаването на обекти от метал. Основният прийом в тази ситуация е работната субстанция да се подава под формата на прахуляк, който да се разтопява посредством лазер или волтова дъга. За да се защищити металът от оксидиране, замърсяване във въздуха или - още по-лошо - от детонация, този развой би трябвало да се прави в херметични камери, цялостни с неподвижен газ. Постигането на нещо сходно в огромни мащаби обаче е много комплицирано и може да се окаже извънредно скъпо начинание.
Въпреки това 3D принтирането на железни обекти напредва. Един от способите за това е потреблението на огромни роботи, оборудвани с MIG електрожени. MIG е редуциране от metal-inert gas. При тази технология работната субстанция се подава под формата на жица, която минава през дюзата на електрожена. От едната страна тя е закачена за източник на високо напрежение и когато бъде допряна до железна повърхнина, се разтопява под въздействието на образувалата се волтова дъга. По време на процеса през дюзата на електрожена минава поток от неподвижен газ, като да вземем за пример аргон, който пази метала, до момента в който се втвърдява.
За да трансформира електрожена в 3D принтер, роботът неведнъж прави заваряване на еднакъв сектор, полагайки един върху различен пластове разтопен метал. Въпросният развой се употребява от MX3D – холандска компания за триизмерно печатане, за основаването на разнородни железни предмети. Както може да се чака за компания от Нидерландия, става дума за леки алуминиеви рамки за колела и даже за 12-метров пешеходен мост, направен от неръждаема стомана и инсталиран над канал в Амстердам.
Базираната в Лос Анджелис компания Relativity Space пък употребява огромни " електорженни " 3D принтери за направата на части за галактически ракети. Всяко от тези устройства се зарежда с жица, направена от алуминиева сплав. Принтерът я разтопява, употребявайки високотемпературна плазмена волтова дъга, след което поставя метала на пластове, защитавайки ги със бликам неподвижен газ. " 3D отпечатаните ракети могат да се създават по-бързо и ще са направени от по-малко елементи спрямо стандартните ", настояват от Relativity Space. Компанията има огромни упоритости. Първите й ракети ще бъдат употребявани за извеждане на спътници в Космоса, само че нейните създатели се надяват, че един ден индустриалната апаратура, наречена Stargate, ще може да основава галактически апарати непосредствено на повърхността на Марс.
Така че, в случай че се чудите на какво са способни 3D принтерите, даже небето не е пределната граница.
2019, The Economist Newspaper Limited. All rights reserved
Всичко това обаче скоро може да се промени. Изследователи от университета в Мейн сега организират тествания с 8-метрова патрулна лодка, основана от нулата единствено за 72 часа. Те реализират това, употребявайки великански 3D принтер.
Абонирайте се за Капитал Четете безкрайно и подкрепяте напъните ни да пишем по значимите тематики Откакто влизат в комерсиално произвеждане през 90-те години на предишния век, 3D принтерите по принцип се употребяват за основаването на дребни предмети като прототипи, съставни елементи за реактивни мотори или зъбни коронки. В момента идва ред на устройствата с големи размери. Те са способни да отпечатват доста по-големи обекти, в сравнение с беше допустимо до момента. И го вършат по-бързо.
За да основат патрулната лодка за потребностите на американската войска, екипът в Мейн работи в съдействие с Националната лаборатория Оук Ридж в Тенеси, която оказва помощ в създаването на процеса по триизмерно печатане и с компанията Ingersoll Machine Tools в Илинойс, която конструира самия принтер. Изследователите от университета са уверени, че потреблението на сходни огромни устройства в корабостроенето ще понижи доста индустриалните разноски и времето за основаване на нови плавателни съдове.
Размерът има значение
Максималният размер на обекта, който може да бъде генериран от даден 3D принтер, се дефинира от размера на самите отпечатващи устройства. В момента множеството от тях са най-вече с размерите на домакински ледник.
През последните няколко години инженерите опитват с разнообразни начини за реализиране на по-големи мащаби при триизмерното печатане, като инсталират механизма върху външно скеле. За жал крайният резултат нормално е постепенно и непрецизно устройство, което генерира груби обекти, нуждаещи се от доста спомагателна и скъпа ръчна обработка.
Учените от университета в Мейн обаче преодоляват този проблем. Те инсталират дюзата, която поставя пластовете от " 3D мастилото ", върху рамка на подемен кран. Самото мастило съставлява разтопена термопластична смола, съдържаща карбонови влакна. Контролирана благодарение на мощен компютър, дюзата се движи хоризонтално (както при всеки развой по триизмерно принтиране) и построява стремежи обект, като генерира тъничък пласт от субстанцията, изчаква го да се втвърди, издига се малко нагоре, поставя още смола и продължава по този метод, до момента в който реализира окончателната форма.
Всичко това може да бъде реализирано със забележителна скорост. Принтерът, конструиран от университета в Мейн, е кадърен да употребява до 70 кг термопластична смола на час. В момента той може да основава предмети с дължина 30 метра, широчина 7 м и височина 3 м. Тези пропорции обаче елементарно могат да бъдат увеличени, като устройството се инсталира на по-голям подемен кран. Също по този начин върху преносимата част, където е инсталирана дюзата, може да се добави и автоматизирана фреза, която да отстранява грапавините и да изглажда повърхността.
След като към този момент са създали технологията, сега учените се пробват да подобрят естеството на триизмерното " мастило ", тъй че да го създадат по-щадящо околната среда. Вместо да употребяват карбонови влакна, те считат да се извърнат към отпадъчната целулоза като сурогат. Подобно решение би спечелило поддръжката на " зелените " деятели, защото карбоновите влакна нормално се създават въз основата на петролни артикули. Хабиб Агхер, който е един от ръководителите на плана, твърди, че задачата е градивната субстанция за печатане да е най-малко 50% на основата на дървесни артикули. Според него по този начин може да се сътвори композитна сплав, която е съизмерима като издръжливост и тегло с алуминия. В близко бъдеще откривателите също по този начин се надяват да могат да поставят до 230 кг 3D мастило на час. Последното им достижение е отпечатването на отливка за основаването на тавана на лодка. За задачата са употребявани целулозни влакна и смола, извлечена от царевични боклуци. И с цел да има спомагателен " зелен " резултат, матрицата може да бъде рециклирана и материалите да се употребяват наново.
Просто натисни print
Създаването на отливки и индустриални принадлежности ще е значимо приложение на огромните 3D принтери, твърди доктор Крейг Блу, шеф по енергийната успеваемост в лабораторията " Оук Ридж ". Производството на принадлежности е скъпа активност заради две аргументи. То изисква профилирани умения, а също така предметите се създават в единични бройки или дребни количества, тъй че не може да се реализира спестовност от мащаба. При триизмерните принтери обаче цената на численост е почти една и съща, без значение дали произвеждаш един или доста предмети.
Технологията предлага и други преимущества. Например принтерът, конструиран от " Оук Ридж ", е употребен от подизпълнители за основаване на особено завършени матрици за бетонни отливки върху фасадата на 45-етажна постройка, издигната на мястото на остарелия захарен цех в Бруклин, Ню Йорк. По принцип сходни матрици се вършат от дърво. За основаването им се наемат експерти, който ги създават ръчно. Въпросните дървени матрици обаче не са изключително издръжливи и се амортизират след 3-4 бетонни отливки. Според доктор Блу обаче 3D отпечатаните аналози, направени от подсилени карбонови влакна, могат да устоят до 200 заливания с цимент.
Лабораторията " Оук Ридж " също по този начин работи по технология, която разрешава директното печатане на бетонни структури. Но защото би трябвало да се употребяват големи 3D принтиращи подемни кранове, основаването на небостъргачи и други сходни уреди с огромни размери явно би трябвало да става не на веднъж, а на части. Отпечатването на бетонни секции в следена фабрична среда и по-късно сглобяването им на място евентуално ще се окаже по-подходящо, изключително когато става дума за направа на комплицирани артистични структури.
Това е методът, общопризнат от Сю Вайгуо и сътрудниците му от университета " Цинхуа " в Пекин. Те употребяват чифт роботизирани " ръце ", посредством които генерират сглобяеми секции от цимент, разбъркан с полиетиленови нишки. След това бетонните панели са употребявани за построяването на 26-метров пешеходен мост над езеро в индустриалната зона на Шанхай. Съоръжението е конструирано по този начин, че да прилича моста " Анджи " – каменна арка над река Киаохе, провинция Хебей, датираща от към 600 година сл. н.е. Репликата на античния мост е отпечатана за към 450 часа. Това е много умерено движение по стандартите на 3D принтера, употребен в корабостроителницата в Мейн, само че много бързо на фона на 10-те години, които са били нужни за построяването на оригинала, и даже спрямо бързината на актуалната строителна промишленост. Изследователите са пресметнали, че индустриалните разноски са били към 2/3 от цената на аналогично оборудване, направено благодарение на стандартен способи. Най-трудната задача, с която 3D принтирането се сблъсква, е основаването на обекти от метал.
Все по-големи обекти и по-висока скорост на печатане се реализират и посредством други технологии за 3D принтиране. Чад Миркин и сътрудниците му в Северозападния университет в Илинойс са създали способ, наименуван high-area rapid printing (HARP). Тяхното устройство е способно да основава обекти с повърхност на основата към един квадратен метър и височина 4 м. То реализира това, като последователно " изтегля " плътния обект от дребен басейн, цялостен с течен полимер.
Въпросният принтер е основан на действителен индустриален развой, само че в по-големи мащаби. При него течният полимер се съхранява в съд с транспарантна основа. Всеки пласт от предмета, който би трябвало да бъде отпечатан, се прожектира през нея с ултравиолетови лъчи. Те от своя страна провокират химична реакция и сгъстяване на полимера в нужната форма. Готовият пласт се захваща за апарат, спуснат към повърхността на течната субстанция, и се изтегля нагоре. Процедурата се повтаря, до момента в който целият подготвен обект не бъде изтеглен от басейна с течен полимер.
Иновацията, която HARP прибавя към този развой, е прибавянето на тъничък филм от смазка, който тече по повърхността на транспарантната основа. Според откривателите субстанцията прилича течен тефлон и пречи на полимерите да се залепят за долната част на басейна, а също по този начин лишават топлината, която се генерира при ултравиолетовото сгъстяване. Крайният резултат от това е, че 3D принтерът е кадърен да работи доста по-бързо от преди. Според доктор Миркин той може да сътвори за няколко часа обект с размерите на възрастен човешки субект. Ако употребявате стандартен тримерен принтер, същото би лишило няколко дни.
Процесът HARP разрешава потреблението на необятен диапазон от материали за печатане в огромен мащаб – става дума за стотици типове разнообразни полимери, които могат да основават твърди, меки или пък гумени обекти. С него могат да се отпечатват и предмети от смоли, съдържащи материали като силициев карбид, който може да се трансформира в твърди термоустойчиви керамични сплави. Компоненти, направени от сходен материал, могат да бъдат употребявани в най-различни промишлености – изработката на коли, самолети, даже и здания. Технологията може да бъде употребена и в още по-големи мащаби, прибавя доктор Миркин. Той също по този начин е съосновател на компанията Azul 3D, която се пробва да комерсиализира процеса HARP. Според неговите упования първите принтери, употребяващи тази технология, ще се появят на пазара след към 18 месеца.
Хеви метъл
Най-трудната задача, с която 3D принтирането се сблъсква, е основаването на обекти от метал. Основният прийом в тази ситуация е работната субстанция да се подава под формата на прахуляк, който да се разтопява посредством лазер или волтова дъга. За да се защищити металът от оксидиране, замърсяване във въздуха или - още по-лошо - от детонация, този развой би трябвало да се прави в херметични камери, цялостни с неподвижен газ. Постигането на нещо сходно в огромни мащаби обаче е много комплицирано и може да се окаже извънредно скъпо начинание.
Въпреки това 3D принтирането на железни обекти напредва. Един от способите за това е потреблението на огромни роботи, оборудвани с MIG електрожени. MIG е редуциране от metal-inert gas. При тази технология работната субстанция се подава под формата на жица, която минава през дюзата на електрожена. От едната страна тя е закачена за източник на високо напрежение и когато бъде допряна до железна повърхнина, се разтопява под въздействието на образувалата се волтова дъга. По време на процеса през дюзата на електрожена минава поток от неподвижен газ, като да вземем за пример аргон, който пази метала, до момента в който се втвърдява.
За да трансформира електрожена в 3D принтер, роботът неведнъж прави заваряване на еднакъв сектор, полагайки един върху различен пластове разтопен метал. Въпросният развой се употребява от MX3D – холандска компания за триизмерно печатане, за основаването на разнородни железни предмети. Както може да се чака за компания от Нидерландия, става дума за леки алуминиеви рамки за колела и даже за 12-метров пешеходен мост, направен от неръждаема стомана и инсталиран над канал в Амстердам.
Базираната в Лос Анджелис компания Relativity Space пък употребява огромни " електорженни " 3D принтери за направата на части за галактически ракети. Всяко от тези устройства се зарежда с жица, направена от алуминиева сплав. Принтерът я разтопява, употребявайки високотемпературна плазмена волтова дъга, след което поставя метала на пластове, защитавайки ги със бликам неподвижен газ. " 3D отпечатаните ракети могат да се създават по-бързо и ще са направени от по-малко елементи спрямо стандартните ", настояват от Relativity Space. Компанията има огромни упоритости. Първите й ракети ще бъдат употребявани за извеждане на спътници в Космоса, само че нейните създатели се надяват, че един ден индустриалната апаратура, наречена Stargate, ще може да основава галактически апарати непосредствено на повърхността на Марс.
Така че, в случай че се чудите на какво са способни 3D принтерите, даже небето не е пределната граница.
2019, The Economist Newspaper Limited. All rights reserved
Източник: capital.bg
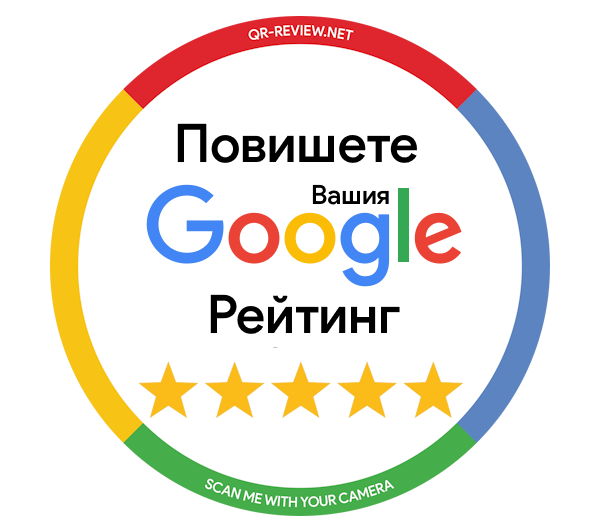

КОМЕНТАРИ