Дигиталните близнаци. Новата „суперсила“ на производителите на автомобили
Експертите настояват, че цифровите близнаци, които сплотяват виртуалния и физическия свят, могат да понижат разноските, да съкратят времето за стартиране на пазара и да обезпечат безвредна работна среда.
През декември 2021 година необичайно създание стартира да обикаля из заводите на Audi, като им оказва помощ да се приготвят за бъдещето.
Спот, роботизирано куче, създадено от Audi и NavVis, немски стартъп, носи 3D лазерен скенер, който записва изображения на всеки инструмент и квадратен метър. Изображенията ще бъдат слети, с цел да се сътвори дигитален близнак на фабриката, който може да се употребява за обмисляне на производството, промяна на инструменталната екипировка и осъществяване на голям брой други усъвършенствания на успеваемостта и понижаване на разноските.
Тъй като Спот може да работи през уикендите без да се оплаква и не се нуждае от обедни почивки, той може да сканира цялата фабрика за 48 часа – задача, която би лишила на екип от хора три седмици.
„ Обединяването на всички данни за обмисляне в нашия цифров близнак ни даде повсеместен взор върху бъдещите ни индустриални проекти за години напред “, споделя Андрес Колер, началник на екипа за виртуално обмисляне на сглобяването в Audi.
Спот, тестови план, може да е изпреварил времето си с няколко години – множеството автомобилни производители разчитат на други способи за сканиране, с цел да цифровизират заводите си – само че цифровите близнаци се обрисуват като ключ към бързото, безвредно и дейно произвеждане, изключително когато автомобилните производители се надпреварват да бъдат в крайник с трендове като електрификацията и софтуерно дефинирания автомобил.
КАКВО Е ДИГИТАЛЕН БЛИЗНАК?
Международната организация по стандартизация (ISO) дефинира цифровия близнак за задачите на индустриализацията като „ цифрово показване на наблюдаем индустриален детайл със синхронизация сред детайла и неговото цифрово показване “.
Използвайки близнаци, производителите на коли могат да проиграят преустройството на цех с мотори с вътрешно горене за произвеждане на електрически коли. Те могат да тестват нова част от инструменталната екипировка, да обучат служащите на нови процеси и да трансформират тези процеси в придвижване, с цел да подобрят коефициента на продуктивност и даже качеството на колите.
„ Когато имате цифров близнак, можете да вършиме неща във виртуалния свят, преди да поемете скъпоструващия риск да ги извършите във физическия свят “, споделя пред Automotive News Europe Ричард Керис, вицепрезидент по създаването на платформата Omniverse в Nvidia. Според него един дигитален близнак, който дава отговор на действителността до последната гайка, болт, развой и служащ в индустриалната мрежа, може да даде на автомобилния производител „ суперсили “.
Nvidia работи с BMW, General Motors, Mercedes-Benz и други по своята платформа Omniverse, която Керис разказва като операционна система на индустриална метавселена. Той бързо добави, че „ метавселена “ в промишлен подтекст „ не е всеки, който се движи в близост като аватар “, а по-скоро мрежа, която разрешава безпроблемна връзка сред 3D виртуални светове.
„ Ключовото нещо за цифровия близнак е, че той не стопира, когато сте го създали “, сподели Керис. „ С течение на времето можете да изучавате и да научавате неща – може би има способи да обучавате роботите да се движат по-ефективно или по-безопасни способи за напредване на оборудването. “
Дигиталните близнаци и по-широката идея за индустриална метавселена се основават на правилата на така наречен промишленост 4.0, която има за цел да построи по-добри процеси посредством събиране („ Интернет на нещата “) и обработка на данни.
Пробив през силозите
„ Първата вълна на Индустрия 4.0 донесе бистрота и известна предсказуемост, само че не съчетаваше действителни данни и опция за симулация “, споделя Пиер Баньон, вицепрезидент, световен началник на акселератора за умна промишленост в Capgemini, пред Automotive News Europe. „ Все още има доста силози. “
В автомобилната промишленост цифровите близнаци могат да разрушат стените сред създаването на артикули – сфера на дизайнерите и инженерите – и процесния инженеринг, където колите минават от първообраз към произвеждане, сподели Баньон, който е работил в Robert Bosch повече от 15 години.
„ Това, за което мечтаехме, беше идеално приспособен за произвеждане продуктов дизайн “, сподели сътрудника на Багнон Матиас Айзеншмид, вицепрезидент, началник на отдела за автомобилно произвеждане и ръководство на веригата за доставки в Capgemini Invent Германия и деец от планирането на производството в Mercedes-Benz. Цифровите близнаци са „ смяна на играта “ за този случай на приложимост, сподели той, като разрешават продуктът и процесът да се развиват по синхронизиран, успореден метод.
„ Получавате индустриална линия, която е зряла през цялото време “, сподели Айзеншмид. „ В предишното трябваше да похарчите доста време и пари във физическото произвеждане, с цел да развиете и оптимизирате процесите. Използвайки промишлен дигитален близнак, можете да идентифицирате и решите множеството от проблемите си авансово във виртуалната фаза. “
Дигиталните близнаци могат да съкратят времето за стартиране на пазара с 20 до 30 %, да подобрят качеството с 20 % и успеваемостта на ресурсите с до 40 %, споделят Баньон и Айзеншмид. „ Това е мащабът на упоритостите, които нашите клиенти влагат, с цел да оправдаят вложенията “, сподели Багнън.
„ Това е инвестиция за доста милиони долари, само че по-важният въпрос е какво ще се случи, в случай че не го извършите? “ Ейзеншмид сподели: „ Ако не създадем това, което би трябвало да се направи, ще се наложи да създадем това. „ Има нови съперници, които към този момент се възползват в забележителна степен от тези нови технологии като общи принадлежности. “
Renault Group основава своя лична индустриална метавселена, включваща цифрови близнаци – развой, който се състои от четири стъпки и продължава години. „ Искаме да разполагаме с изцяло използвана галактика с цялостно копие на това, което се случва в действителния свят “, съобщи пред Automotive News Europe Ерик Марчиол, шеф „ Цифрова промяна “ в Renault Group.
„ Научихме, че всеобщото потребление на данни е най-хубавият метод за реализиране на нашите цели “, сподели Марчиол.
Renault има амбициозни цели: До 2025 година тя чака да реализира общи икономии в размер на 320 млн. евро, икономии на инвентар в размер на 260 млн. евро, 60-процентно редуциране на времето за доставка на колите и 50-процентно понижаване на индустриалните излъчвания на CO2. По отношение на качеството ще има главен принос за 60-процентно понижаване на гаранционните разноски.
Но пътят на Renault към цялостна индустриална метавселена демонстрира обсега на подобен план.
Първата стъпка, събирането и стандартизирането на данни, стартира през 2016 година, когато Renault сътвори свои лични приложения, с цел да може да пресъздава съществуващите данни в индустриалния завод на таблети, което докара до някои „ бързи победи “, сподели Марчиол. След това е основан вътрешен екип, който да „ разгадае какво има вътре “ в програмируемите логичен контролери, роботите и „ черните кутии “ в другото съоръжение.
При съществуването на 10 000 робота в групата от разнообразни снабдители като Comau или Kuka, както и на машини отпреди десетилетия, „ имахме голямо многообразие от данни “, сподели Марчиол.
Сега, сподели той, Renault може да събира данни от оборудването си по типов метод – и получава по един милиард набора от данни дневно. „ Но не е задоволително, в случай че се събират данни единствено от оборудването, тъй като към момента имаме доста ръчни интервенции “, добави Марчиол. За да събира тези данни, Renault е построило цифрови работни станции, които наблюдават човешките придвижвания.
БЛИЗНАК ЗА ВСИЧКО
Извън индустриалния развой цифровите близнаци играят значима роля в създаването на артикули.
Дизайн: Екстериорните и интериорните дизайнери стартират процеса с виртуални модели, като се стигне до напасване и довеждане докрай и интериорни материали.
Инженеринг: Въз основа на дизайнерските чертежи инженерите основават дигитален модел на физическия автомобил, в това число всички съставни елементи, платформа и каросерия.
Валидиране и тестване: Тестовете за конфликт, симулациите на шофиране и тестванията в аеродинамичен тунел са единствено някои от приложенията на цифровия двойник.
Следпродажбено обслужване, съгласуваност и актуализации: Цифровите близнаци също дават опция за актуализации по въздуха.
Производство: Според специалистите в близко бъдеще продуктът и производството ще се създават взаимно благодарение на цифрови близнаци.
На втория стадий Renault основава цифрови близнаци на своите фабрики, употребявайки технологии на Siemens и Dassault, с цел да симулира ново съоръжение, и сканира съществуващите си фабрики до последния милиметър. След това Renault разполага с аватар, който може да употребява за образование за конфигурация на оборудването или ергономичност.
След това Renault наблюдава всички изходящи и входящи действия от доставчиците, „ тъй че да знаем тъкмо къде се намира всеки камион “, споделя Марчиол. Това уголемява екосистемата от данни на Renault отвън личния й промишлен отпечатък.
В четвъртата стъпка. Renault ще употребява мощта на своята индустриална метавселена в цялата група посредством основани в облака, лесни за потребление аналитични принадлежности. „ Демократизираме потреблението на принадлежности за огромни данни вътре във всички наши интервенции “, сподели той.
Дигиталните близнаци и други елементи на метавселената са от решаващо значение за прекосяването на Renault към електрически коли и задвижващи системи, които ще се създават в границите на отделената компания Ampere в група фабрики в Северна Франция, наречена ElectriCity.
„ Когато стартираме нови процеси за електрически мотор или батерия, не можем да отнемем шест месеца, с цел да достигнем цялостен потенциал или оптимизация на процеса “, споделя Марчиол.
Той чака Renault да разполага с изцяло функционална метавселена до две години, като последната стъпка ще бъде затварянето на автоматизиран цикъл за противоположна връзка, който да разреши параметрите на съоръжение като роботи или преси да бъдат променяни благодарение на цифрови близнаци.
Такива близнаци към този момент се употребяват за моделиране на нови индустриални линии, в това число програмиране на роботи и осъществяване на инспекции за сигурност във виртуална действителност, „ преди да се похарчи даже 1 евро “, сподели Марчиол.
Неочаквани изгоди
Renault откри, че събирането на данни може да докара до непредвидени резултати.
„ Започнахме с концепцията, че можем да спестим доста пари с планирана поддръжка, и го направихме, само че това не е най-големият източник на доходи “, споделя Марчиол. „ Когато започнете да събирате данни от цялото си съоръжение и развиете поредност в процеса, сте в положение да видите слона в стаята, който не сте могли да видите преди. “
За Renault това включва проблеми с качеството в каросерийния завод, които могат да бъдат проследени до равнището на съответна спойка, или закъснение на процеса от съответен робот при настройка на автомобил, който може да се спуска по линията единствено един път на три часа.
„ Същите данни, които могат да се употребяват за планирана поддръжка, могат да се употребяват за качество или ползване на сила “, споделя Марчиол. „ Всеки път, когато прибавяме съоръжение, не е належащо да се питаме: „ Трябва ли да събираме данни? “ Това е автоматизирана политика. “
Марчиол добави: „ В момента, в който се прави разбор на данните, е належащо да се направи разбор на данните: „ Отворихме кутията на метавселената, само че би трябвало да я използван на всички места с повече функционалности. “
Други производители на коли разчитат на цифровите близнаци за повишение на успеваемостта, нововъведенията и понижаване на разноските. GM, в съдействие с General Electric, е създал по този начин нареченото тестово място за виртуална фабрика, с цел да моделира процесите за произвеждане по поръчка; цифровите близнаци също по този начин тестват интеграцията на физическите и осведомителните системи в завода.
Мерцедес, който Керис дефинира като един от „ основните “ клиенти на Nvidia, ще работи с доставчика, с цел да построи цифров близнак на фабриката си в Ращат, Германия, където от 2024 година ще се създават напълно електрически коли от клас „ entry-luxury “ на идната платформа MMA. С помощта на цифровия близнак Mercedes може да тества внедряването на платформата и нейните принадлежности и процеси, без да прекъсва съществуващото произвеждане.
BMW, сходно на Mercedes, разчита на цифрови близнаци (и работи с Nvidia), защото приготвя фабричната си мрежа за произвеждане на напълно електрически – както и софтуерно дефинирани – коли. Моделът iFactory има за цел „ да направи планирането и симулацията на всички процеси и цялата индустриална система 100 % виртуални “, съобщи автомобилният производител през юни предходната година.
„ Производственото обмисляне може да интегрира виртуалния артикул във виртуалната фабрика на ранен стадий “, съобщи в известие Микеле Мелхиоре, началник на индустриалната система, цеха за принадлежности за обмисляне и построяването на фабрики в BMW. „ Това понижава напъните за обмисляне и финансовите разноски и в това време подсигурява, че процесите са по-ефективни и по-стабилни по време на разгръщането на производството. “
Заводът на BMW в Регенсбург към този момент е напълно цифрово картографиран, а неговият цифров близнак се употребява за обмисляне на бъдещите структури и конфигурации на завода. Сред другите фабрики на BMW с цифрови близнаци са американският цех в Спартанбург, Южна Каролина, и заводът в Мюнхен.
BMW съобщи, че ще приключи цифровото сканиране на всички свои фабрики до „ началото на 2023 година “ в партньорство с NavVis, която с изключение на в кучето робот Спот е профилирана в мобилни лазерни скенери, които операторите прикрепят към тялото си, до момента в който се движат из индустриалните пространства.
„ Насочваме се в посока на визуализация на фабриката в действително време “, споделя Филип Куадстеге, старши управител на решения за цифрови заводи в NavVis.
Скенерите на NavVis снимат оборудването в цеха в точната му позиция, само че също по този начин и физическото пространство към инструментите до тавана. Това може да дефинира какъв брой място остава за нови принадлежности, което е от решаващо значение, в случай че производителите на коли желаят да разширят производството.
Новите принадлежности са общоприетоо снабдени със лично цифрово изображение, споделят Куадстеге и други специалисти, само че по-старото съоръжение би трябвало да се сканира парче по парче.
„ Повечето от данните, с които разполагат фирмите, са извънредно остарели “, сподели той пред Automotive News Europe. „ Много компании към момента работят в 2D формат. “ Дори новите принадлежности би трябвало да бъдат сканирани, откакто бъдат сложени на място, сподели той, защото проектът на обекта може да се разграничава от действителната апаратура, което прави цифровия близнак неакуратен.
След като заводът бъде сканиран, NavVis основава дигитален близнак благодарение на облачна технология.
Куадстеге споделя, че прозрачността – опцията всеки, където и да е в компанията, да вижда какво се случва в цех, който може да е на хиляди километри – е главният фактор за изгодите от цифровите близнаци.
„ Има огромен капацитет, в случай че се вкара бистрота “, споделя той. „ Можете да намалите вложенията, качеството на продуктите се покачва, покачва се успеваемостта при планирането. “
Тъй като заводите се конкурират между тях за систематизиране на транспортни средства и вложения, сходна бистрота може да се преглежда като опасност, сподели той. „ Мениджърите на фабрики се тормозят за своя цех спрямо другите “, сподели той. „ Но въпреки това, не можете да избегнете дигитализацията. “
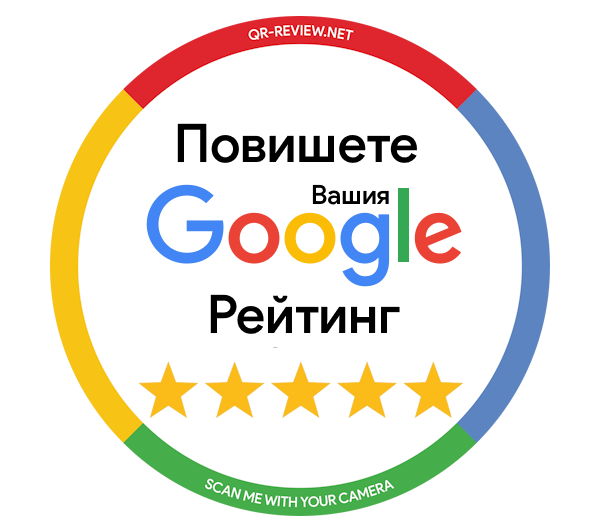
